Introduction
Acoustic emission testing (AET) is a well-established non-destructive testing (NDT) technology commonly used to detect fatigue cracks in steel and composite pressure vessels, above ground atmospheric storage tanks, and steel and concrete bridges. Acoustic emission testing is characterized as a passive NDT technique since it does not insert some type of energy into the structure to interrogate for material anomalies. The structure must be stressed to a level that causes the fatigue crack to grow. As the fatigue crack grows in the micrometer range, or even less, acoustic emission is emitted from the fracturing material. Acoustic emission is simply a set of ultrasonic waves that that travel through material. AE makes it way to sensors mostly via longitudinal, shear, surface, and guided waves.
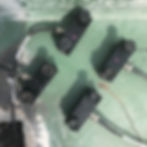
Figure 1. Acoustic emission array of sensors placed around an existing bridge fatigue crack.
Acoustic Emission Structural Loading
Listed below are some common methods to stress an asset during an acoustic emission inspection:
Steel pressure vessel AE testing: Vessel is pressurized hydrostatically or pneumatically to 5/3 or 1.1 times the service pressure, respectively.
Composite pressure vessel AE testing: Vessel is pressurized hydrostatically or pneumatically to 1.5 or 1.1 times the service pressure, respectively.
Aboveground storage tanks AE testing: Vessel is recommended to be tested a 50% or greater capacity to stimulate corrosion product activity or leakage activity.
Steel bridge AE testing: Steel railway bridges are preferably stressed with freight trains with particular emphasis on correlating AE activity to heaviest cars – usually the locomotive.
The acoustic emission test sequence is generally defined in the relevant ASTM, ASME, API, or DOT standards that oversee the fabrication and in-service examination requirements.
Bridge Testing with Acoustic Emission
The objective of acoustic emission testing of steel bridges with existing cracks, or recently repaired cracks, is to determine if the crack is active or inactive. If it is active, at what rate may it be potentially growing? Figure 1 shows an array of four acoustic emission sensors places around a crack tip on a steel bridge girder. While as few as three sensors may be used to location the location of the crack growth, it is advisable to use more if possible, to improve AE source location.
A properly conducted AE test will use intelligent filtering processes to eliminate non-relevant acoustic emission. Spatial filters are used via acoustic emission guard sensors to prevent AE from outside the array from influencing the test results. While not observable in Figure 1, and acoustic emission guard sensors was placed outside the array adjacent to a riveted joint in an attempt to filter out fretting related AE.
The rate and intensity of acoustic emission from fatigue cracks primarily used to assess whether the crack is active or inactive. If the crack is active, a more sophisticated analysis may be applied to determine the crack growth is active or critically active. The acoustic emission rate is largely based upon how many AE events are detected per load cycle. The load cycle depends on the type of asset tested but should be normalized by the duration of the test, number of AE sensors, etc. Acoustic emission intensity is used to assess the severity of the crack and is quantified through amplitude (dB), AE strength, AE energy, and AE duration. The acoustic emission rate and intensity are considered using a severity ranking matrix.
The first short video below illustrates how an array of 4 acoustic emission sensors detects and displays locatable AE events in 2-D. The red squares are acoustic emission events that were located by their respective arrival times at AE sensors 1-4.
Figure 2: Generic acoustic emission detection and location of fatigue crack on steel bridge.
The second short video illustrates how AE software may be used to import a scaled image of the tested structure to superimpose the AE events onto the image.
Figure 3: Structural specific acoustic emission detection and location of fatigue crack on steel bridge.
Summary
Fatigue cracks develop in most steel bridges. To determine the if the cracks is active or passive, advanced inspection methods may be used at the discretion of the bridge engineer. The additional information may be used decide at a specific fracture-critical location whether no further repair action is required, the location should be monitored more frequently than scheduled inspections, or how soon funds should be allocated for repair or replacement. In such a case, acoustic emission may be used to classify the severity of fatigue cracks in fracture-critical members.
References
1. Ledeczi, A., P. Volgyesi, E. Barth, A. Naas, A. Pedchenko, T. Hay, and S. Jayaraman, "Self-sustaining Wireless Acoustic Emission Sensor System for Bridge Monitoring", New Developments in Sensing Technology for Structural Health Monitoring, vol. 96: Springer Berlin Heidelberg, pp. 15-39.
2. Lédeczi, A., Völgyesi, P, Nádas, A., Barth, Eric, Pedchenko, A., Hay, T.R., and S. Jayaraman, Self-sustaining wireless acoustic emission system for bridge monitoring, Lecture Notes in Electrical Engineering, ISSN 1876-1100.
3. Hay, T.R., Jayaraman, S., Ledeczi, A.,Volgyesi, P., Al Sammane, G., Wireless Technology for Steel Bridges, NDE/NDT for Highways and Bridges ASNT Conference Proceedings, Oakland Ca.
4. Hay, T.R., Jayaraman, S., Inspection of Submerged Bridge Pile from Above the Water Line, NDE/NDT for Highways and Bridges ASNT Conference Proceedings, Oakland Ca.
5. Hay, T.R., Hay, D.R., Hay, J.R., Greve, David W., Oppenheim, Irving J., “Transforming Bridge Maintenance from Time-Based to Predictive Maintenance using Acoustic Emission MEMS Sensors and Artificial Intelligence,” 7th World Congress on Rail Research, Montreal, Canada.
6. Hay, T.R., Hay, D.R., Plotkin, D., C..M. Lee, and Rose, J.L., “Rail Defect Detection Under Shelling,” 7th World Congress on Rail Research, Montreal, Canada.
7. Hay, T.R., Hay, D.R., “High Speed – Low Cost Rail Inspection Technology,” 7th World Congress on Rail Research, Montreal, Canada.
8. David W. Greve, D. Robert Hay, Hay T.R., Irving J. Oppenheim, Didem Ozevine, Stephen P. Pessikif, and Nathan L. Tyson, Structural Tests using a MEMS Acoustic Emission Sensor, SPIE Smart Structures Conference Proceedings, 2006.