Leak Testing: Non-destructive Testing Options
- Thomas R. Hay, Ph.D., P.E
- Dec 7, 2023
- 5 min read
An overview of Bubble Leak Testing, Pressure Change Leak Testing
Leaks are common occurrences in pressure vessels, piping systems, hydraulic systems, and pneumatic systems. The leaks may be caused by material defects, mechanical stresses, seal failure, wear and tear, temperature changes, over pressurization, fatigue, corrosion among other mechanisms. To prevent leaks at pressurized boundaries, regular inspections, maintenance, and testing are essential. Non-destructive testing (NDT) methods, such as ultrasonic testing, pressure change testing, or mass spectrometer leak testing, can be employed to detect and locate leaks before they become critical. Additionally, adhering to proper installation, operation, and maintenance practices and ensuring that materials and components are suitable for the intended pressure and conditions can help mitigate the risk of leaks.
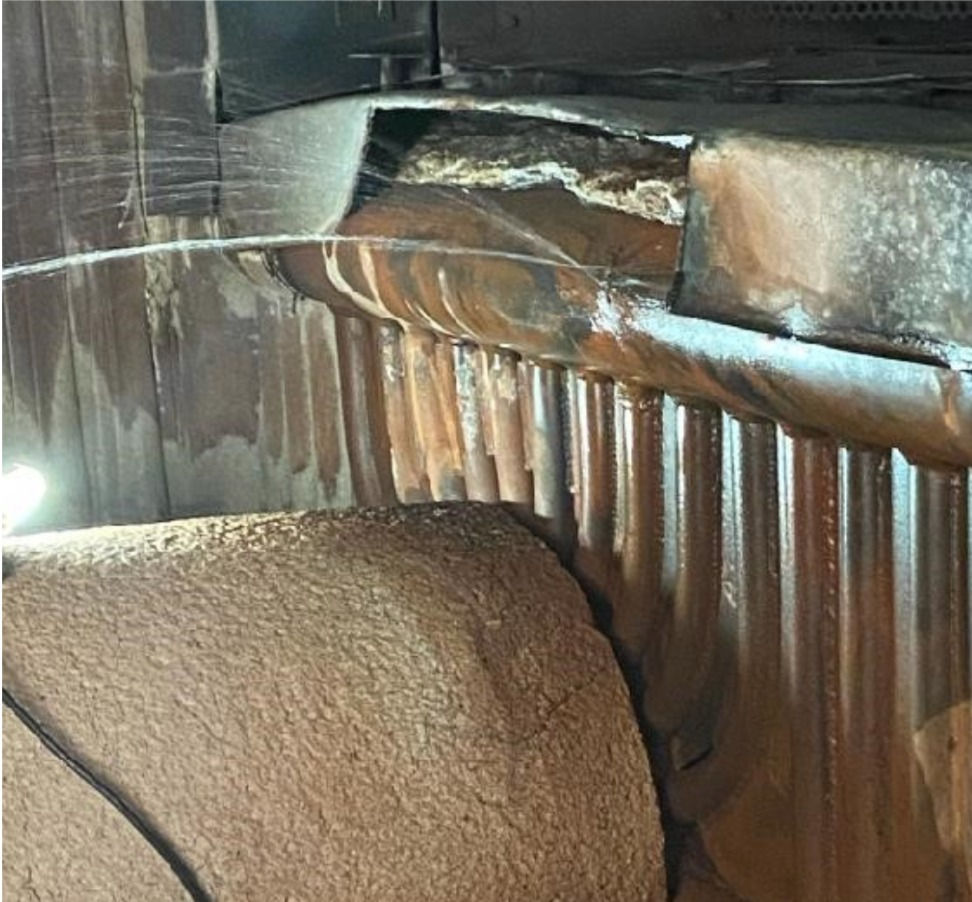
Bubble Leak Testing
Bubble leak testing is a non-destructive testing (NDT) method used to identify leaks or defects in sealed or pressurized components, such as pipelines, tanks, or pressure vessels. The principles of bubble leak testing involve the following:
- Introduction of Pressure: The first step in bubble leak testing is to introduce a specific pressure (usually air or another gas) into the component being tested. This pressure creates a driving force that can force any contained gas or liquid to escape through leaks or defects in the material.
- Submersion in a Liquid: The pressurized component is then submerged in a liquid, typically water. The water serves as a medium for visualizing the escaping gas or liquid.
- Observation of Bubbles: As the pressurized gas or liquid escapes from any leaks or defects, it forms visible bubbles in the surrounding liquid. These bubbles can be small or large, depending on the size and severity of the leak.
- Inspection and Evaluation: Trained inspectors carefully observe the component while it is submerged, looking for the presence of bubbles. The location, size, and frequency of bubbles are all important factors in assessing the integrity of the component.
- Leak Detection and Localization: The detection of bubbles allows inspectors to identify the presence of leaks or defects. Further evaluation can help localize the exact location of the leak, which is valuable for repair or maintenance purposes.
- Sensitivity and Verification: The sensitivity of the test can be adjusted by varying the pressure, the type of liquid used, and other factors to ensure that even small leaks or defects are detected. The process may also involve verification steps to confirm the findings and assess the severity of the defects.
Bubble leak testing is a relatively simple and cost-effective method for detecting leaks and defects in a wide range of components. However, it is important to note that it may not be suitable for all applications, and the sensitivity and accuracy of the test can depend on various factors, including the size and shape of the component, the choice of testing medium, and the expertise of the inspectors.
Pressure Change Leak Testing
Pressure change leak testing is a non-destructive testing (NDT) method used to detect leaks or defects in sealed or pressurized components by monitoring changes in pressure. The principles of pressure change leak testing involve the following:
- Pressurization: The first step is to pressurize the component being tested with a gas, typically air or another suitable medium. This pressurization creates a differential pressure between the inside and outside of the component, which can force gas to escape through any leaks or defects.
- Stabilization: After pressurization, the system is allowed to stabilize for a predetermined period. During this time, the pressure inside the component should remain relatively constant if there are no leaks.
- Pressure Monitoring: Monitoring equipment, such as pressure gauges or sensors, continuously measures the pressure inside the component throughout the testing process. Any change in pressure over time can indicate the presence of a leak.
- Test Duration: The test duration can vary depending on the specific application and requirements. Longer test durations may be necessary to detect smaller or slower leaks.
- Acceptance Criteria: Establishing acceptable pressure change criteria is crucial. These criteria define how much pressure change is considered acceptable before a component is deemed defective. This criteria is often determined based on the sensitivity required for the application and industry standards.
- Data Analysis: Recorded pressure data is analyzed to identify any deviations from the expected stable pressure. If a pressure drop is detected beyond the acceptable criteria, it suggests a potential leak or defect.
- Localization and Repair: Once a pressure change is identified, additional testing or inspection methods may be employed to localize and pinpoint the exact location of the leak. This information is valuable for repair or maintenance purposes.
- Calibration and Validation: It's essential to calibrate and validate the testing equipment regularly to ensure accuracy and reliability of the results. This includes checking the accuracy of pressure gauges and verifying that the testing system is functioning correctly.
Pressure change leak testing is a versatile method used in various industries, including manufacturing, aerospace, automotive, and more, to assess the integrity of sealed components. It is suitable for both high-pressure and low-pressure applications and can be used to detect leaks in various types of materials, including metals, plastics, and ceramics. The sensitivity and accuracy of the test depend on factors such as the pressure range, testing equipment, and the skill of the operators.
Mass Spectrometer Leak Testing
Mass spectrometer leak testing is a specialized non-destructive testing (NDT) technique used to detect and locate leaks in sealed components or systems, often in applications where high sensitivity is required. The principles of mass spectrometer leak testing involve the following:
- Vacuum System: Mass spectrometer leak testing typically takes place in a vacuum chamber or system. The component or system to be tested is placed inside this vacuum environment.
- Gas Introduction: A tracer gas, such as helium or another suitable gas with a low molecular weight and good diffusivity, is introduced into the component or system. The tracer gas will escape through any leaks or defects present.
- Ionization: Inside the vacuum chamber, the introduced tracer gas is ionized. This is usually achieved by bombarding the gas molecules with high-energy electrons, causing them to become positively charged ions.
- Mass Separation: The ionized tracer gas ions are then subjected to a mass spectrometer. The mass spectrometer separates the ions based on their mass-to-charge ratio (m/z). Since helium is commonly used as the tracer gas in leak testing due to its small atomic mass, any helium ions detected in the mass spectrometer are indicative of a leak.
- Detection: The mass spectrometer detects the helium ions, and the intensity of the helium signal is monitored. When a leak is present in the component or system, helium ions will be detected at the corresponding m/z values, and the signal will increase above the baseline.
- Leak Localization: Mass spectrometer leak testing can provide information about the size and location of the leak. By using multiple sensors or by analyzing the time it takes for the helium ions to reach the mass spectrometer, the exact location of the leak can often be determined.
- Sensitivity: Mass spectrometer leak testing is highly sensitive and capable of detecting extremely small leaks, often in the range of 10^-9 to 10^-12 standard cubic centimeters per second (sccs), depending on the instrument and conditions.
- Quantitative Analysis: The concentration of helium ions detected in the mass spectrometer can be used to estimate the leak rate, allowing for quantitative assessment of the leak severity.
Mass spectrometer leak testing is commonly used in industries where precise leak detection is crucial, such as semiconductor manufacturing, aerospace, and the production of high-pressure systems. Its high sensitivity and ability to detect leaks in complex or sealed systems make it a valuable NDT technique for critical applications.
Summary
In summary, the choice of leak detection method depends on factors such as the size and type of leaks you need to detect, the industry, and the level of sensitivity required. Bubble leak testing is simple but less sensitive, pressure change leak testing offers versatility, and mass spectrometer leak testing provides exceptional sensitivity for critical applications where even tiny leaks must be identified.
Yorumlar