Magnetic Particle Testing
- Thomas R. Hay, Ph.D., P.E
- Jun 14, 2021
- 4 min read
Updated: Feb 10, 2022
Non-Destructive Testing: Magnetic Particle Testing (MT, MPI)
Magnetic particle testing (MT) is a fast, simple, and cost effect non-destructive testing technique that is capable of finding discontinuities in ferromagnetic metals. Compared to other non-destructive testing techniques, magnetic particle testing is the most reliable at finding surface and near surface discontinuities. Magnetic particle testing can detect inherent discontinuities such as ingot pipe, cold shuts, and hot tears as well as processing discontinuities such as seams in rolled bar and laminations in rolled plate. Lastly, magnetic particle testing is capable of finding in service discontinuities as well such as fatigue cracks that are caused by cyclically applied stress. Magnetic particle testing has four application methods, wet fluorescent, dual light, wet visual, and dry visual. The particles used in each method are made of a combination of iron and iron oxide with high permeability and low retentivity. Dry application particles are larger than wet applications with their particles being between 0.002” and 0.006” while wet method particles range from 0.0002” to 0.0006”. Each method has its own advantages and disadvantages and which method you choose for inspection is determine by a variety of factors.
Wet fluorescent magnetic particle (WFMT) testing is a non-destructive testing technique that uses magnetic particles suspended in either water or light oil distillate that has a high flash point. The media that the magnetic particles are suspended in reduce friction between the particles and the test surface allowing for greater particle mobility along the test surface. Greater particle mobility, even particle application, and the ability to find smaller cracks are all advantages of WFMT. To ensure all these advantages, the technician must confirm that their particle concentration is within the accepted parameters of American Society for Testing and Materials E709-08 Standard Guide for Magnetic Particle Testing (ASTM E709-08). The equipment needed to perform wet fluorescent magnetic particle testing include a source of magnetizing force, method of dispersion for the particles, and an ultraviolet inspection light. Because of the need to reduce the ambient light at the surface of the test piece, generally wet fluorescent magnetic particle testing is done inside or somewhere where the ambient light levels can be kept below 2-foot candles or 20 lux. If it is not possible to control the ambient light levels, a dry visible application will have to be implemented.
Dry visible magnetic particle testing is a non-destructive testing technique that is the preferred method used when ambient light levels cannot be kept under 2 food candles or 20 lux. Besides being able to be used in higher ambient light levels, some advantages of dry visible magnetic particle testing include use in extreme cold or hot environments, superior particle mobility for relatively deep-seated flaws using half wave rectified current, and easy particle removal from the test surface. The different applications methods of dry visible magnetic particles include a squeeze bottle, powder gun or blower, and compressed air powdered gun. Each method must use an additional squeeze bottle full of air to clean off the excess particles that are not attracted to the flux leakage fields of the discontinuities. Dry visible magnetic particles come in a variety of colors. The color chose for inspection is dependent on which will provide the greatest contrast between the test piece and the dry visible magnetic particles. Dry visible particles have some advantages over wet fluorescent but there is a method called dual light magnetic particles that work in both with both ambient and ultraviolet light.
Dual light magnetic particles can be used in environments where the ambient light cannot be controlled, or it can also be used in environments where the ambient light can be controlled. The product is normally supplied as a ready to use premixed aerosol can or dry powder that can be mixed in either petroleum or water suspensions. Be sure to read to manufacturers requirements to ensure you are using the proper suspension. No matter which of the three methods you are using, it is important to implement quality control checks to ensure your inspection will produce reliable and valid results.
Quality control checks are important when it comes to non-destructive testing. In regard to magnetic particle testing, they assess your magnetic field strength and direction as well as determine if your ambient and UV-A light levels meet the standard set by ASTM E709-08. Shims are an example of a quantitative quality indicator or QQI. They are thin pieces of ferromagnetic metal with a design etched on one side that allows the technician to assess proper magnetic field strength and magnetic field direction. The shim is place face down on the test piece and then the test piece is magnetized. The technician should be able to see part of the etched design depending on the direction of the magnetic field. Another quality control check that is exclusive to a yoke is a weighted test block. Depending on the style of yoke you are using AC or HWDC will determine the weight your yoke must be able to lift to pass the quality control test. For AC yokes the standard is 10 pounds and the HWDC must be able to lift 40 pounds. Being able to lift the weighted test bar will tell the technician that their yoke is producing a sufficient magnetic field to sufficiently magnetize their test piece. Lastly, a light meter needs to be used to assess the level of both ambient and UV-A light at the surface of the test piece. In conclusion, magnetic particle testing is inexpensive and extremely reliable non-destructive testing method used to find surface and slightly subsurface discontinuities.
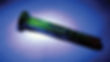
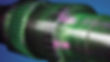
Figure 1.1: Examples of cracks found using wet fluorescent magnetic particle testing.
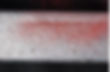
Figure 1.2: Example of a crack found using dry visible magnetic particle testing.

Figure 1.3: Example of the image a technician wants to see after using a shim (QQI) to assess adequate magnetic field strength and direction.

Figure 1.4: Example of a light meter that will assess both ambient and UV-A light levels at the surface of the test piece.
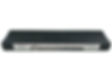
Figure 1.5: Example of a weight test bar for an AC yoke (10 lbs.). A HWDC test bar would just be four of these stacked on top of one another.